How does a print shop evaluate print color quality?
In the pressroom, if you want to evaluate the quality of the color of the printed product, the following three methods are generally used:- Visual Observation
- Densitometer measurement method
Traditional densitometers are mainly used to measure the optical density of the ink layer, which indirectly controls the printing quality by reflecting the concentration of the ink layer, but it does not directly measure the color information. Therefore, the application scope of traditional densitometers is limited. They can only evaluate the thickness and consistency of the ink layer, and cannot conduct a comprehensive analysis of the hue and saturation of the color itself.
The spectrodensitometer makes up for this deficiency. The spectrodensitometer combines the functions of density measurement and color analysis, and can capture the spectral data of color to provide more accurate color information. It can not only measure density, but also analyze the spectral characteristics of color and identify subtle color deviations. Therefore, the spectrodensitometer has more advantages in printing quality control, especially in occasions that require high-precision color management, which can help ensure the color consistency and accuracy of printed products.
- Spectrophotometric Measurement
During the printing process, spectrophotometers can help operators monitor the color consistency and accuracy of printed products in real time. By comparing the spectral data of the target color and the actual printed color, the spectrophotometer can accurately quantify the color difference value and prompt the operator to make timely adjustments. This method is particularly suitable for demanding printing operations, such as brand color consistency control, high-end packaging and artwork reproduction.
In short, the application of spectrophotometer can greatly improve the accuracy of printing quality control and ensure that the color of printed products remains consistent in different batches, different machines, and different light sources.
So, how do you choose the printing quality inspection equipment that suits your pressroom? Let us first have a comprehensive understanding of densitometers and spectrophotometers:
Printing Densitometer
A print densitometer is an instrument used primarily in the printing and packaging industries to measure the optical density of a color. Unlike more general color measurement tools, a print densitometer focuses on analyzing how light is absorbed by a color ink layer, helping to ensure color consistency and quality.
Working principle of printing Densitometer
Print densitometers assess density by measuring the amount of light absorbed or transmitted by a sample. This measurement is usually done by shining a light source through the sample, and a sensor in the device assesses the intensity of the light passing through the sample. Based on the intensity of the light, the print densitometer calculates the optical density, providing a numerical value that reflects the density level of the color.When to use a printing densitometer
Printing densitometers are particularly effective when it is necessary to control the concentration of printed colors, especially in the following situations where they are used more frequently:- During the printing process : The printing densitometer can ensure that the ink concentration of each batch of printed products is within a controllable range to maintain consistency between batches.
- Proofing and printing adjustments : During the print proofing and calibration stage, a densitometer is used to ensure that the ink layer density meets the standard so as to maintain the expected color effect in the formal printing.
- Production quality control : Densitometers are very important in the quality control of printing production. By quickly measuring the concentration of the ink layer, color deviations can be discovered and adjusted in a timely manner.
Spectrophotometer
Spectrophotometers, are versatile devices used to measure color across various industries. Unlike Spectrodensitometers that focus on density, spectrophotometers evaluate a sample's color by examining light reflectance across the visible spectrum. This capability makes spectrophotometers well-suited for industries requiring color precision beyond density measurements .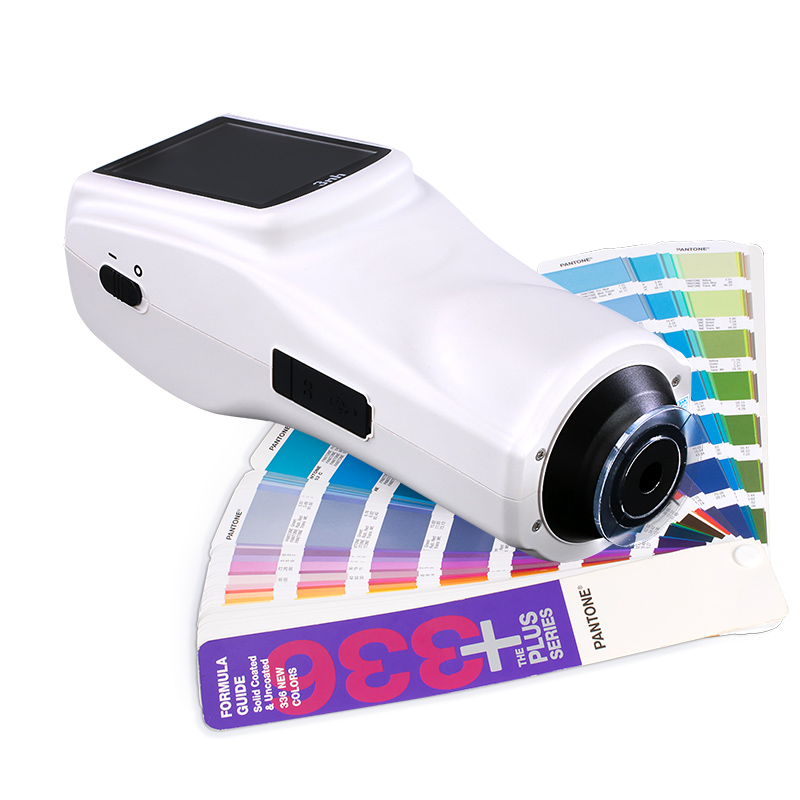
How Spectrophotometers Work
A spectrophotometer works by directing light onto a sample and capturing the reflected or transmitted light across multiple wavelengths. The device records how each wavelength of light interacts with the sample, providing a spectral signature that is then used to calculate the color. By comparing these spectral data points, the device accurately represents the sample's color in terms of chromaticity and luminance.When to Use a Spectrophotometer
Spectrophotometers are suitable for various occasions that require accurate color measurement and color consistency management, especially in the following situations:pressroom : During the printing process, spectrophotometers can help operators monitor the color of printed products in real time to ensure color consistency of each batch. By capturing the spectral data of the printed color, spectrophotometers can detect and quantify color differences and adjust the color in time to make the finished product meet the design and customer standards. It is especially suitable for high-demand printing occasions, such as brand logos, packaging printing and other applications that have strict requirements on color consistency.
Paint and coating production : In paint and coating manufacturing, spectrophotometers are used for precise color matching to ensure that the color of the finished product meets the expected color to avoid color differences between batches and ensure the quality consistency of the product.
Textile dyeing : In the textile production process, spectrophotometers are used to detect the color consistency of dyed fabrics to ensure that each product in mass production meets the expected color standards and meets customers' high color requirements.
In these scenarios, spectrophotometers can provide accurate spectral data support to ensure that products maintain color consistency in different batches and under different production conditions. Especially in pressroom, spectrophotometers are an important tool for achieving high-quality color management.
The difference between a spectrodensitometer and a spectrophotometer
When choosing between a Spectrodensitometer and a spectrophotometer, understanding their fundamental differences can make a significant impact on your choice.Measurement Focus : Spectrodensitometers are density-focused, measuring how much light is absorbed by an ink layer. Spectrophotometers, however, measure full-color information based on light reflectance and transmission.
Precision and Data Output : Spectrophotometers generally provide more detailed data on color, while Spectrodensitometers focus on optical density values, which are crucial in printing but may be insufficient for broader color matching needs.
Spectrodensitometer or spectrophotometer?
Factors to Consider When Choosing
Industry-Specific Needs: For example, printing and packaging sectors may benefit more from Spectrodensitometers , while spectrophotometers serve broader color matching and measurement requirements across various industries.Precision Requirements : Spectrophotometers are generally more precise when complete color data is needed, while Spectrodensitometers are ideal for density measurements in high-volume production.
Ease of Use and Portability : Consider usability and whether a device will need to be transported frequently. Spectrophotometers may have more complex interfaces, while Spectrodensitometers are often more straightforward.
Cost Considerations: Spectrodensitometer vs. Spectrophotometer
While Spectrodensitometers tend to be more affordable and focused on density measurement, spectrophotometers, with their full-color analysis capability, can be more expensive. Evaluate your budget relative to the scope of your color measurement needs.Choosing between a Spectrodensitometer and a spectrophotometer comes down to the specific needs of your industry, the level of color measurement precision required, and budget considerations. While Spectrodensitometers serve well in density-focused tasks, spectrophotometers are ideal for applications needing comprehensive color accuracy.
FAQs
What industries primarily use Spectrodensitometers?
Spectrodensitometers are most commonly used in printing, packaging, and ink production where density measurement is key.
Are spectrophotometers or Spectrodensitometers better for printing?
Spectrodensitometers are often better for printing as they measure color density, which is crucial for maintaining color consistency on printed materials.
How do maintenance needs differ between these devices?
Both devices require regular calibration, though spectrophotometers may require more frequent maintenance due to their complex spectral analysis features.
Can spectrophotometers measure density as well as color?
While spectrophotometers primarily measure color, some models offer basic density measurement; however, they may not be as precise as Spectrodensitometers for density-specific tasks.
What is the role of calibration in Spectrodensitometers and spectrophotometers?
Calibration ensures measurement accuracy. Both instruments require periodic calibration to maintain precision, especially in quality control settings.